Optimizing Control Systems with PLC, RTU, and SCADA
In the ever-evolving world of industrial automation, Programmable Logic Controllers (PLCs) play a crucial role in controlling and monitoring various processes. One of the lesser-known but highly valuable features of PLC programming is the “aging functions.” In this article, we will explore the concept of aging functions, their practical applications, and how they can enhance the performance of your PLC-based automation systems.
I.What Are Aging Functions in PLC Programming?
Aging functions are a set of tools within PLC programming that assist in monitoring the duration and frequency of specific conditions. These functions are particularly useful in managing and controlling processes with time-varying parameters, a common occurrence in many industrial settings. Aging functions essentially track how long a specific condition has been met or unmet and can be programmed to trigger specific actions based on this duration. This provides a valuable mechanism for controlling critical operations.
II. Practical Applications of Aging Functions in PLC Programming
Enhancing Reliability and Safety
- Timing Maintenance with Aging Functions
Aging functions are extremely useful for scheduling maintenance tasks. By monitoring the operating time of various components or machines, maintenance alerts can be triggered when specific thresholds are exceeded. This predictive maintenance approach allows for performing maintenance before equipment failure, reducing downtime and costly repairs. In cases where parallel equipment is in use, the system can automatically decide which one should operate, ensuring close-to-optimal uptime.
- Environmental Control
In applications where precise temperature and humidity control is critical, aging functions can be used to monitor and regulate environmental conditions. For example, in a storage facility with climate control, aging functions can help maintain temperature and humidity settings based on historical data and real-time conditions.
- Batch Processes
Industries such as pharmaceuticals and food processing often rely on batch processes. Aging functions ensure that each step of the production process is completed within specified time frames. If a stage takes too long or is completed too quickly, the PLC can make the necessary adjustments to maintain product quality and efficiency.
III. Implementing Aging Functions in PLC Programming
Implementing aging functions in PLC programming requires a thorough understanding of your specific automation process and a systematic approach. Here’s a general guideline to help you get started:
- Define the Condition
First, clearly define the condition or event you want to monitor. For instance, if you are monitoring the operating time of a pump, the condition could be “pump running.”
- Set Aging Parameters
Specify the time interval and thresholds that make sense for your application. This may involve setting limits for acceptable minimum and maximum operating times.
- Programming Logic
Use aging functions in your PLC program to track the condition and calculate the duration it has been met or unmet.
- Trigger Actions
Based on the aging parameters, program the PLC to trigger specific actions or alarms when certain thresholds are exceeded. These actions could include maintenance alerts, process adjustments, or shutdown procedures.
Let’s create a sample project using aging functions found in the Microdiagram program to illustrate these guidelines.
Aging Manager Blog:
Effect: This is the block activation input.
Count: Indicates how many slave devices will work together simultaneously.
AgingDirection: Up to 10 “Aging Member” blocks can be connected to the output of the Aging Manager block. For example, if 6 “Aging Member” blocks are connected to this output, and the “Count” input is set to 2, these 6 members will work in pairs at 1-minute intervals.
Aging Member Block:
The “Aging Member” block works in conjunction with the “Aging Manager” block. It allows us to put equipment that needs to be run at defined intervals into a periodic cycle. Once the necessary configurations have been made in the input of the “Aging Member” block, the output information for the equipment to be used is determined, such as digital output or output relay.
Sample Application:
Three member blocks are connected to the manager. By setting the “Effect” input of the manager block to 1 and the operating time to 1 minute, the three pieces of equipment will continue to operate in pairs at 1-minute intervals.
IV. Advantages of Using Aging Functions
- Increasing Efficiency and Predictability
Using aging functions in PLC and SCADA systems helps balance the workload of equipment in the system, leading to operational efficiency. Additionally, continuously monitoring aging criteria allows for predictive maintenance and fault prediction.
- Enhanced Control
Aging functions respond to specific time-based conditions, providing a more sophisticated level of control. This leads to more efficient and precise automation.
- Reducing Downtime
Process settings based on predictive maintenance and aging functions can significantly reduce unplanned downtime and maintenance costs.
- Improved Product Quality
In processes where product quality is critical, aging functions ensure that essential steps are completed within the desired time frame, contributing to consistent quality.
V.Real-World Examples
To demonstrate real-world applications of aging functions, consider the following examples:
- Water Treatment Plants
Aging functions monitor water treatment processes and adjust chemical dosages based on the transition times between various treatment stages.
- Water Booster Stations
Aging functions improve energy efficiency and operational efficiency in water booster stations by activating and deactivating pumps based on their performance and operating times.
- Process Automation
In any process automation application with redundant systems, aging functions determine the sequence of operation for backup systems, providing data for energy savings, maintenance, and fault prediction.
VI. Conclusion
Embracing the Future of Automation
Aging functions in PLC programming offer an innovative and intelligent way to enhance your industrial automation processes. By monitoring the duration of specific conditions, aging functions enable predictive maintenance, process optimization, and better control. In an ever-evolving industrial landscape, incorporating aging functions into your PLC programming tools is a step toward more efficient and reliable operations.
Staying ahead in a dynamic industrial landscape means harnessing the power of advanced PLC features such as aging functions. Embrace this technology, and you will see your automation systems perform at their best, reducing downtime and increasing efficiency.
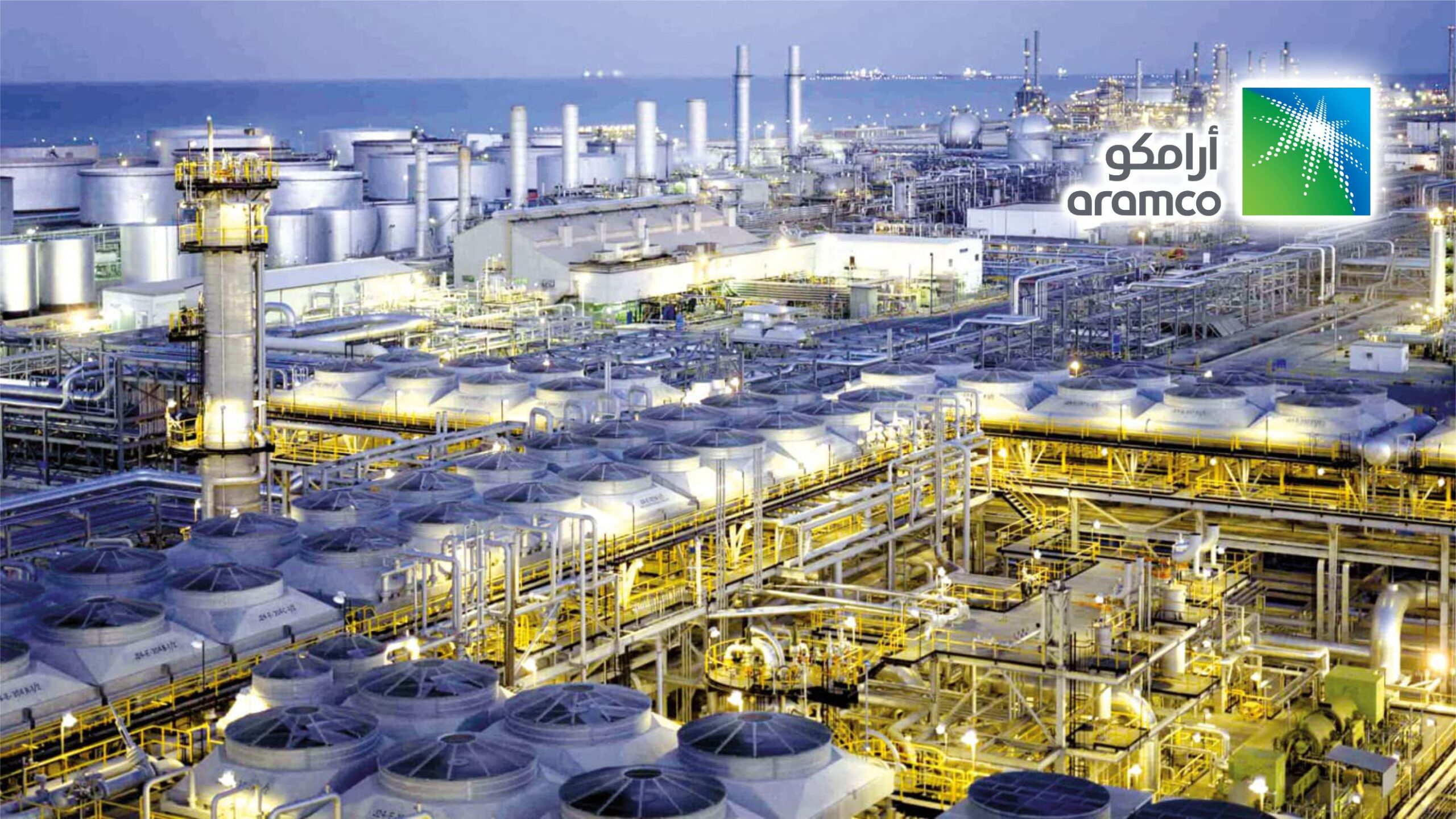
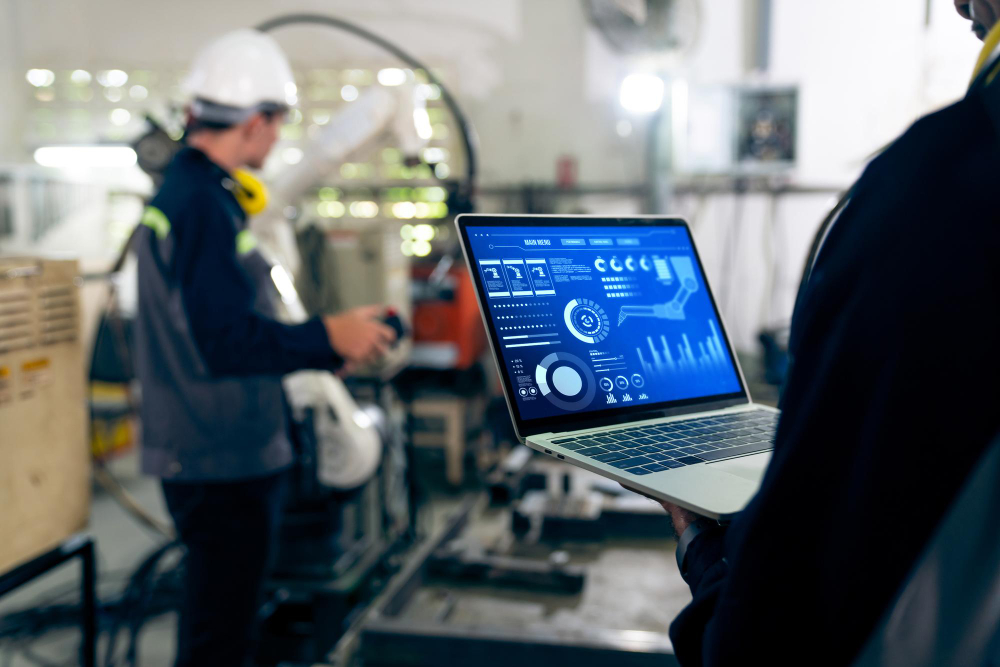
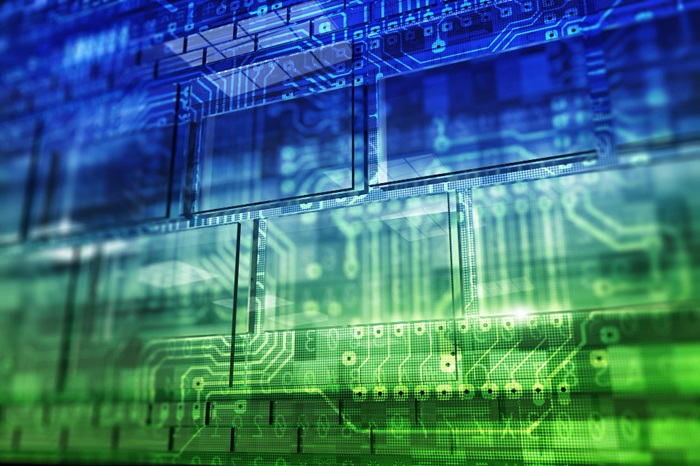
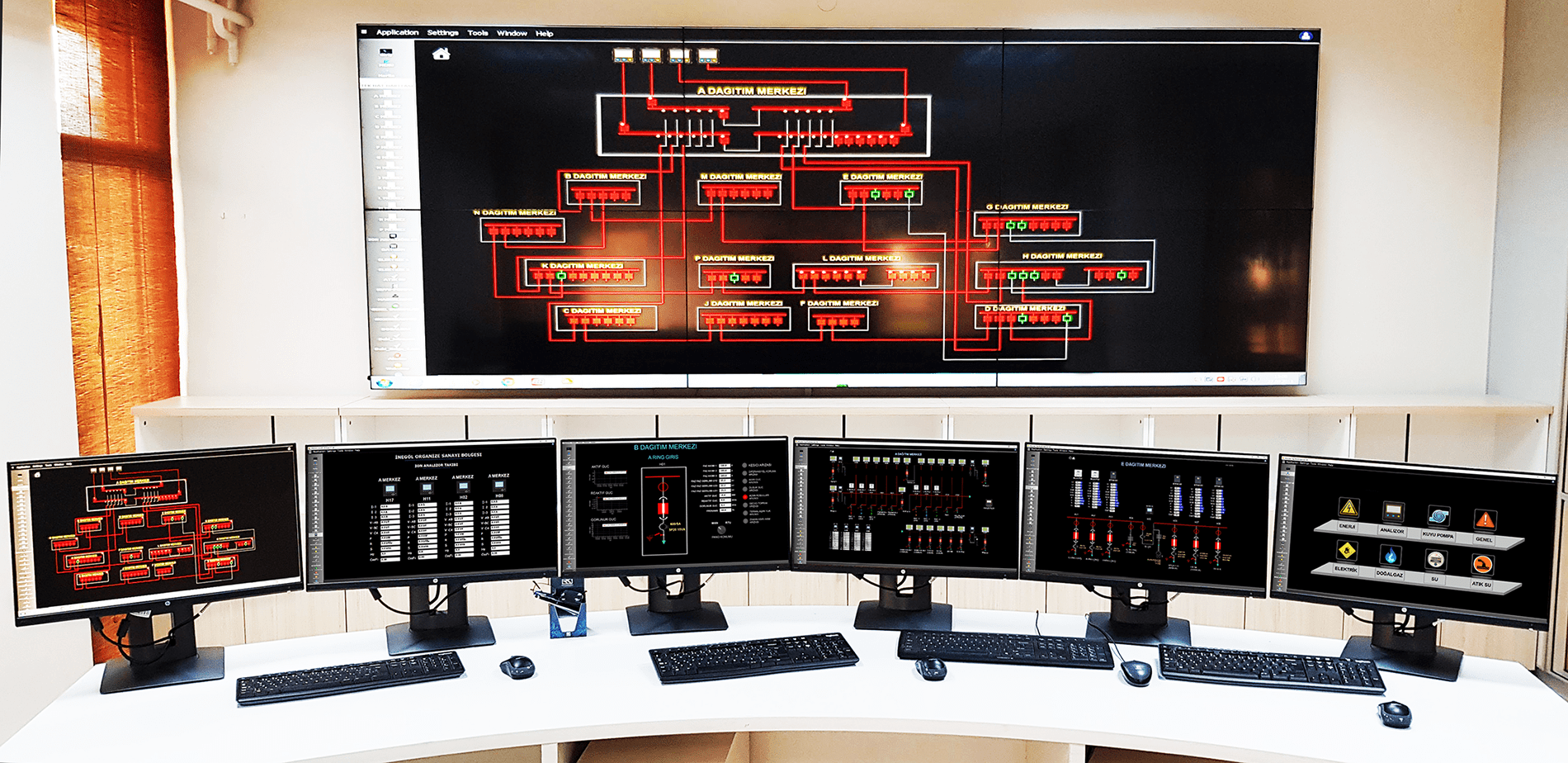
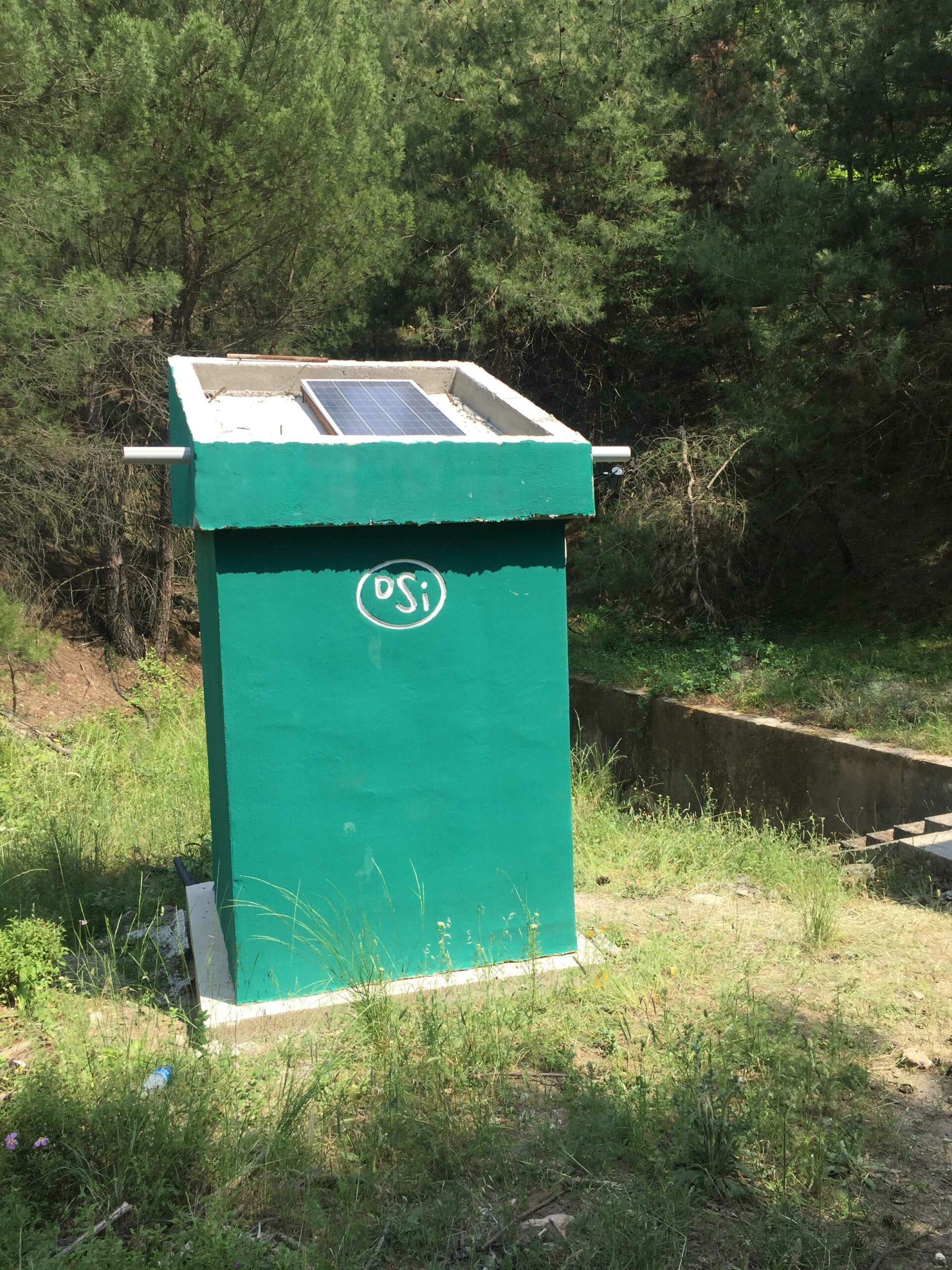
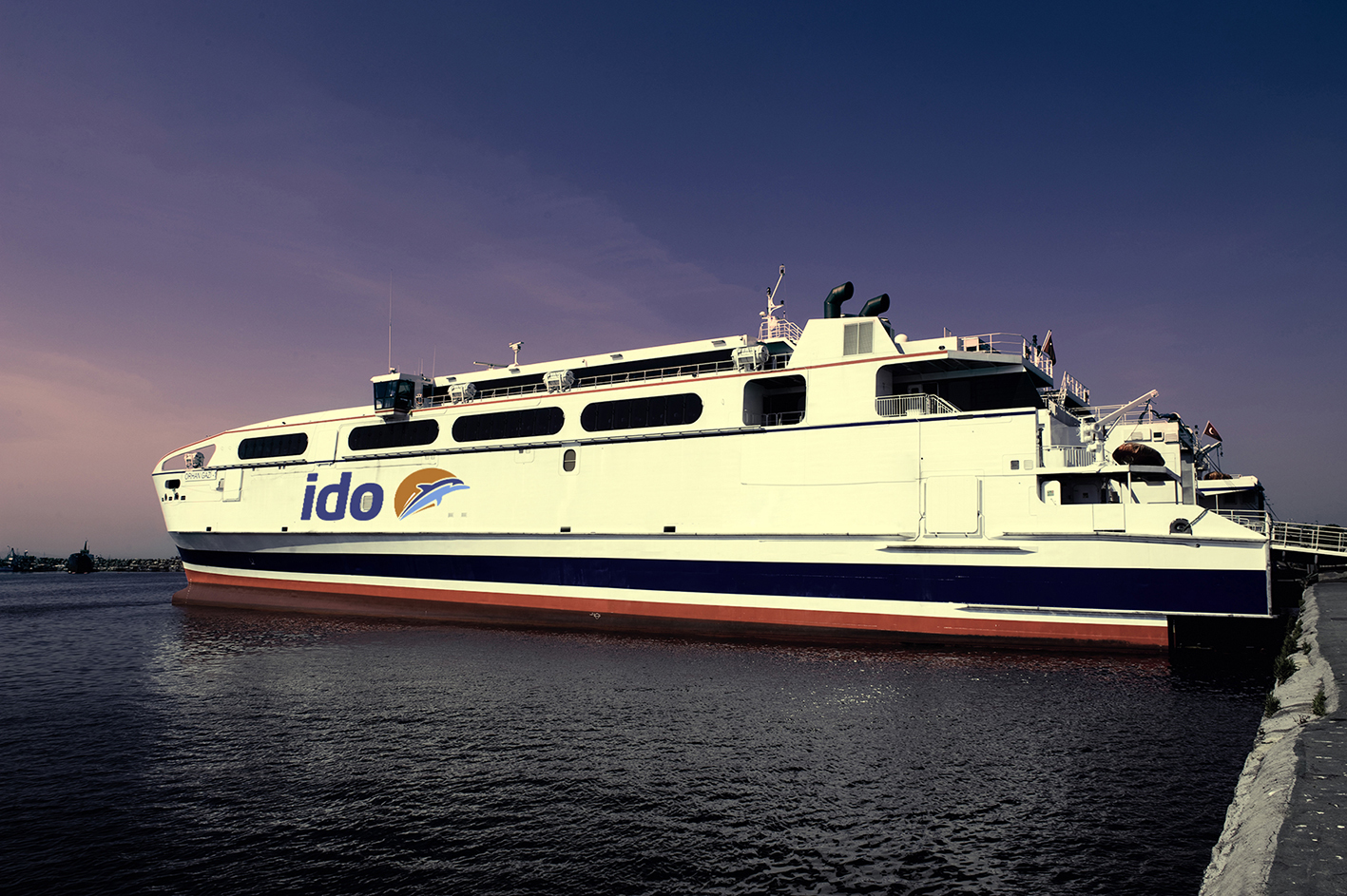
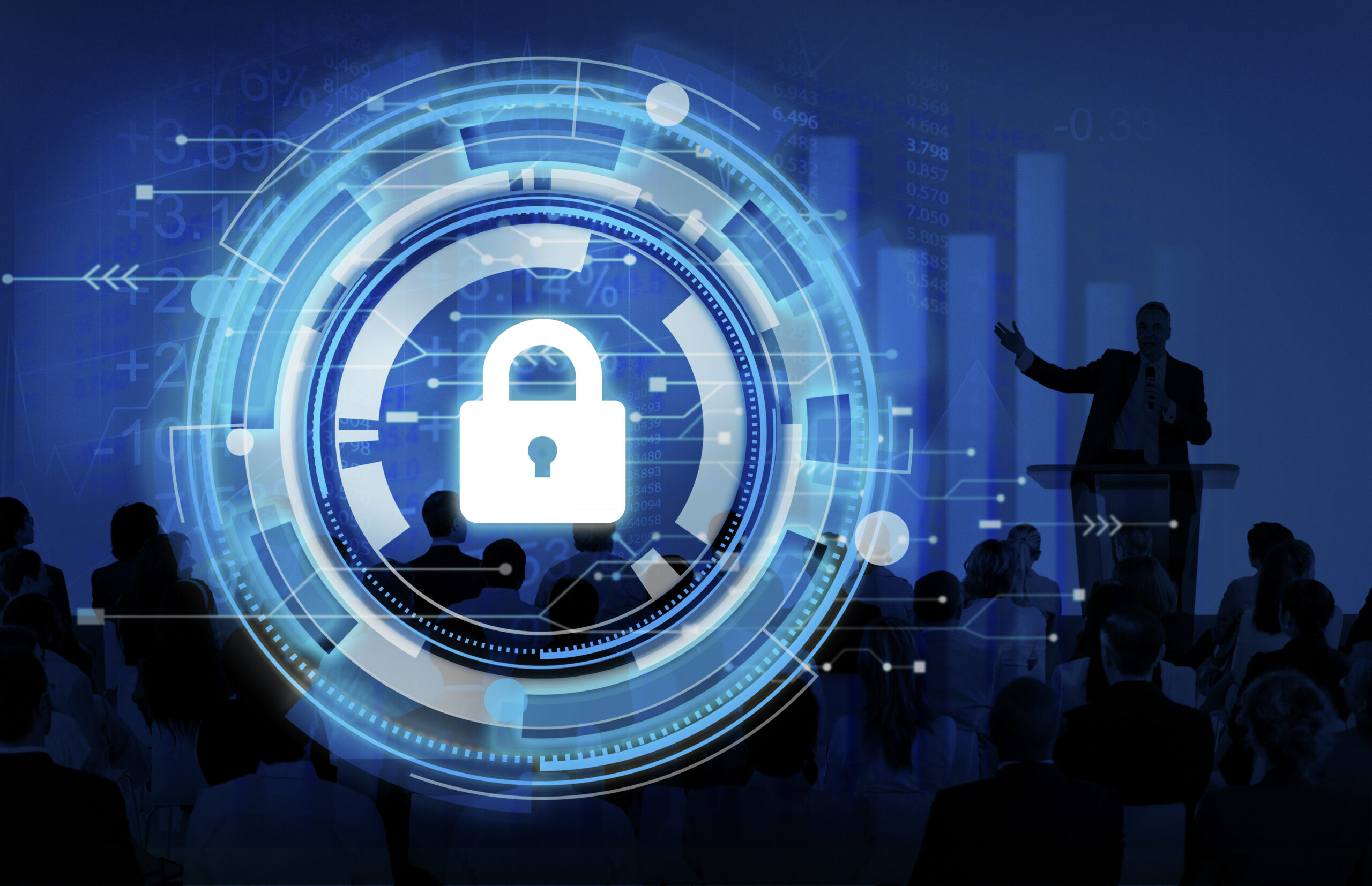
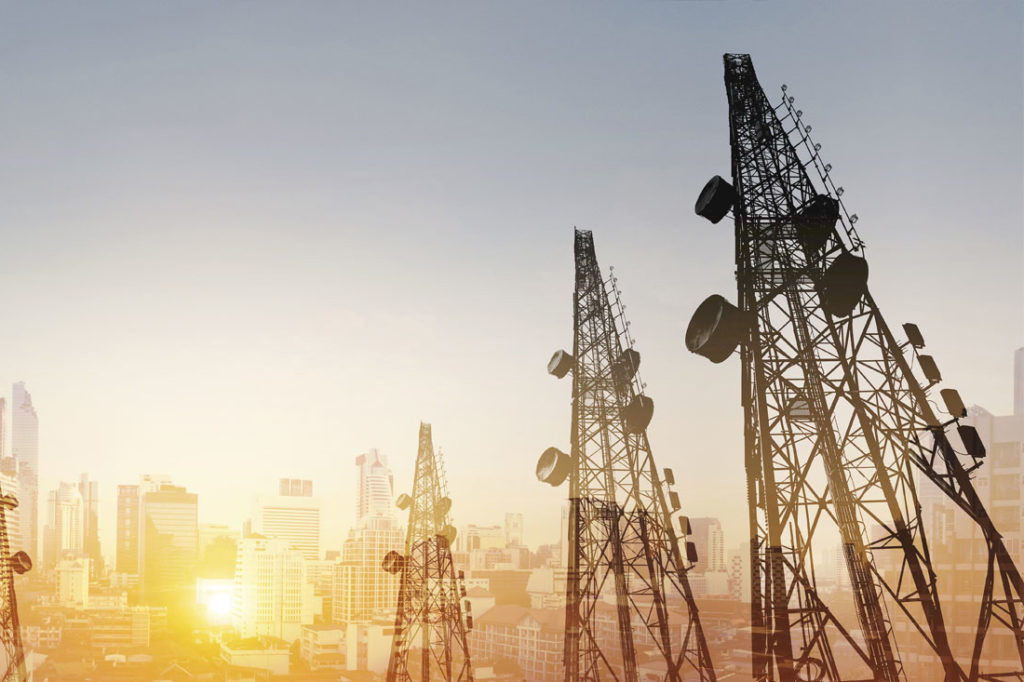
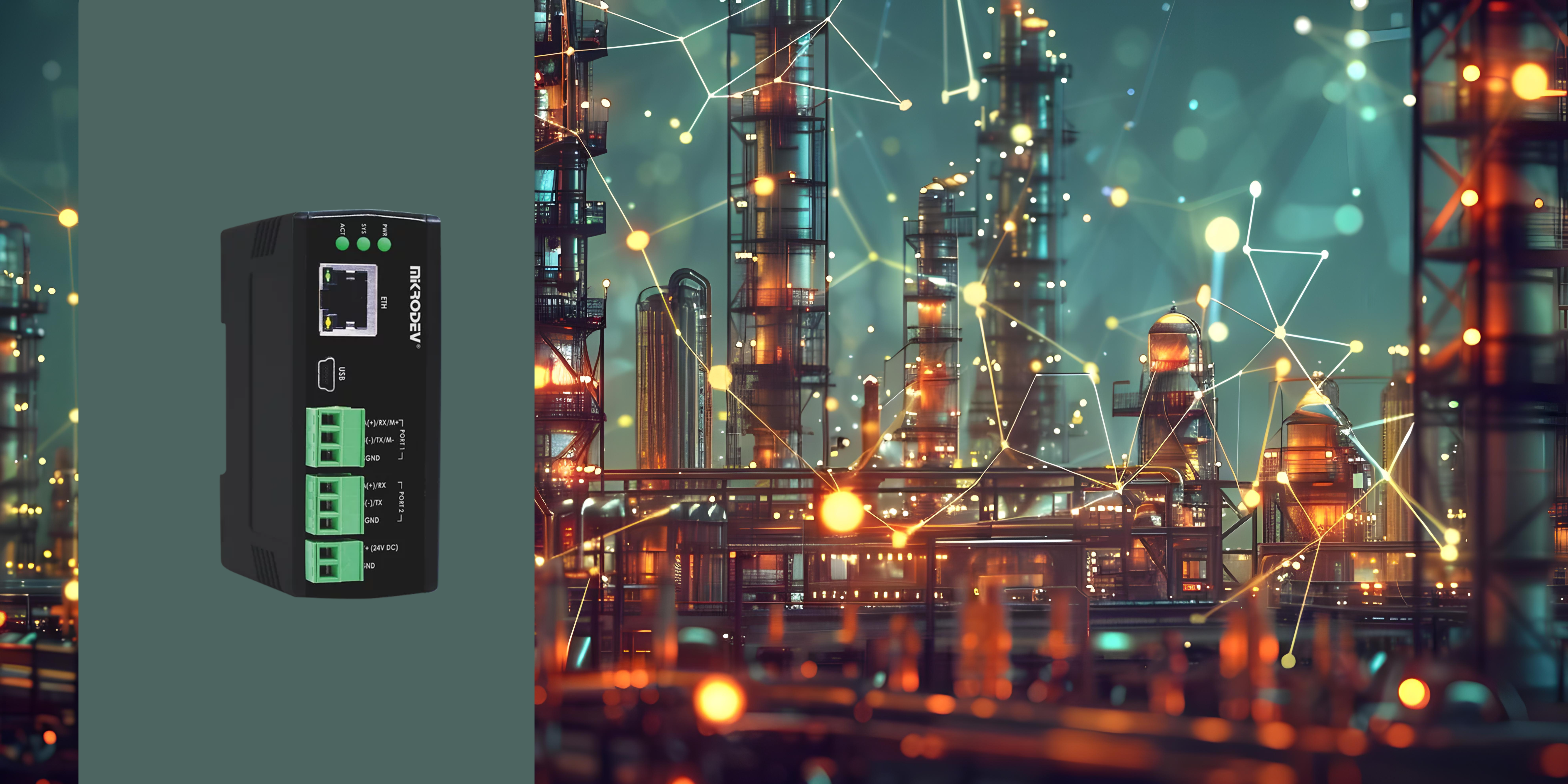
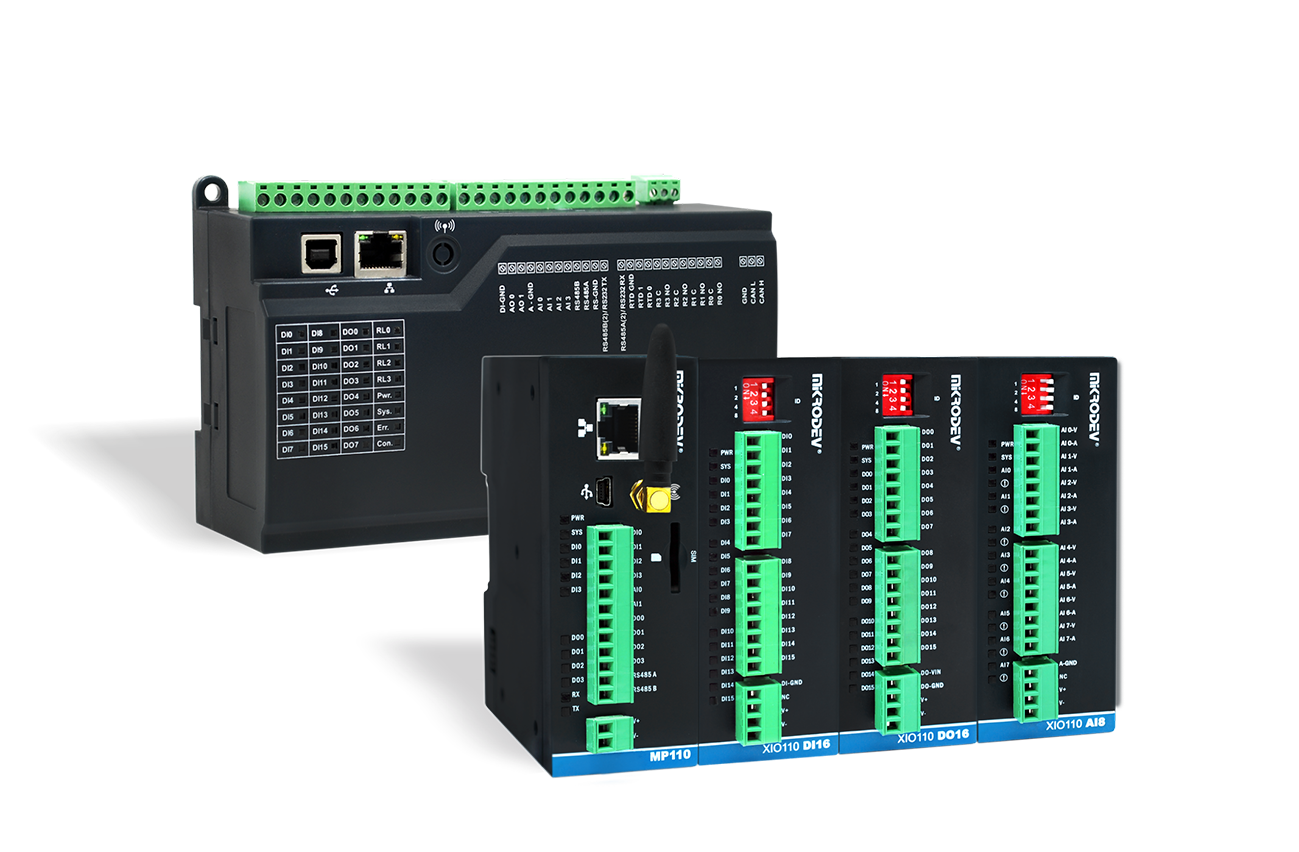